Advancements in 3D Printing of Body Parts Revolutionizing Healthcare
Imagine yourself going to a shop and asking for a replacement for your diseased/damaged tissues or functional organs. Sounds fantastic, like a work of science-fiction, doesn’t it? However, it is a fact today! Printing of body parts is the process of developing bioartificial tissues/organs via an additive manufacturing technique called ‘3D printing/ bioprinting’.
With each passing day, the world is moving towards technological advancements, be it in the automobile industries, in electronics, or even in healthcare. For patients suffering from end-stage organ failure, orthotopic transplantation remains the ultimate clinically approved treatment. It is, however, associated with severe donor shortages, adverse host immune rejection post-transplantation, and/or lifelong requirement of immunosuppression therapy.
Hence, this novel 3D printing technique is a ray of hope, an extraordinary breakthrough & alternative, and has the competence to drive medical research forward. As per the United Network for Organ Sharing, the waiting list of candidates as of 31st of March 2024, is 103,892. Hundreds of thousands of people are actively waiting for a lifesaving organ transplant, out of which only a handful of people will be blessed and unfortunately, the rest may die waiting for the organs. Owing to the limited availability of donor tissues and organs, medical research is heading towards personalized therapeutic strategies. One of which is developing bioartificial tissues/ organs via 3D printing techniques. This promises to play a key role in fabricating tissue-specific analogues.Briefly, 3D printing is an advanced, alternative, versatile, and sophisticated computer-aided design (CAD) based additive manufacturing (AM) technique that works in a layer-by-layer manner, enabling a wide array of materials to be patterned in different shapes and complexities.
Often referred to as rapid prototyping, it provides excellent control over the internal and external architecture of a developed model, which is an essential condition for patientspecific treatment concepts. The historic innovation of the concept of AM was first introduced by Chuck Hull in the 1980s. Further, in the early 1990s, this layer-by-layer technique combining clinical imaging data with CAD based approach was explored at the Massachusetts Institute of Technology, (MIT) using a regular ink jet print head, thereby offering numerous potential opportunities for tissue engineering. The prospect of integrating CAD along with medical scans ensures the potential development of patient tissue/organ–specific personalized and anatomically shaped implants.
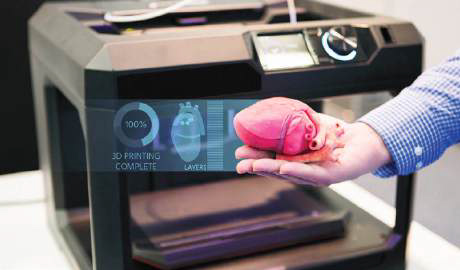
The concept of bioprinting is basically an extension of 3D printing that involves a systematic deposition of liquids or gels encompassing living cells (termed as bioinks) and containing essential growth factors in a pre-defined organized manner, mimicking the native anatomical shapes, to produce bioartificial organs or patient-specific, living tissue on-demand, to imitate their natural counterparts.
Pioneering work in this regard was conducted in Prof. Thomas Boland's laboratory at the University of Texas, employing a simple desktop printer with slight modifications to dispense cells and proteins. Since its debut, 3D printing has been used to fabricate a range of inanimate objects.
Some more applications of 3D printing technology:
• A 3D-printed drug, Spritam® (levetiracetam), a prescribed medicine to treat seizures in children and elders, developed by Aprecia Pharmaceuticals’ binder jet 3D printing technology (ZipDose® Technology), has gained regulatory approval from the Food and Drug Administration for its commercialization. This is an example of a 3D printing technique, used by the pharmaceutical industry, to develop a drug.
• Medical research concerning minimally invasive surgeries includes the fabrication of magnetically controlled implants using shape-shifting materials, as demonstrated by an MIT research team led by Prof. Xuanhe Zhao. For instance, 3D printing of a self-steering catheter that could be guided magnetically through the body to control blood flow, capture images, or deliver drugs at a specific location!
• In food industries as well where companies like Aleph Farms and Steakholder Foods are pioneering in pushing the technology forward to develop easily customizable and alternative edible printed food. For instance, Israel-based Steakholder Foods, which is revolutionizing 3D meat and fish printing technology, has announced the launch of the industry’s first plant-based 3D-printed eel.
However, bioprinting clinically relevant living tissues and organs is undoubtedly the most complicated and challenging endeavor. Globally, scientists are making tremendous progress thereby accelerating this field (Figure 1). In an attempt to get closer to clinically relevant biological implants, a research team led by Prof. Adam Feinberg at Carnegie Mellon University fabricated the largest and the first patientspecific, clinically relevant bioprinted patch via freeform reversible embedding of suspended hydrogels (FRESH) 3D bioprinting technique, using a patient-tissue derived material and exhibited its successful implantation onto the woundsite, targeting soft tissue injury.
Dr. Arturo Bonilla, a San Antonio-based pediatric ear reconstructive surgeon, in collaboration with 3D Bio Therapeutics, demonstrated the successful implantation of a collagen-based 3D-printed outer ear using the patient’s cells. HiMedia Laboratories Pvt. Ltd. | himedialabs.com 13 The patient was born with microtia. Usually, children growing up with congenital defects like microtia or anotia are socially and psychologically impacted. Thus, 3D bioprinting opens new and promising avenues for these patients.
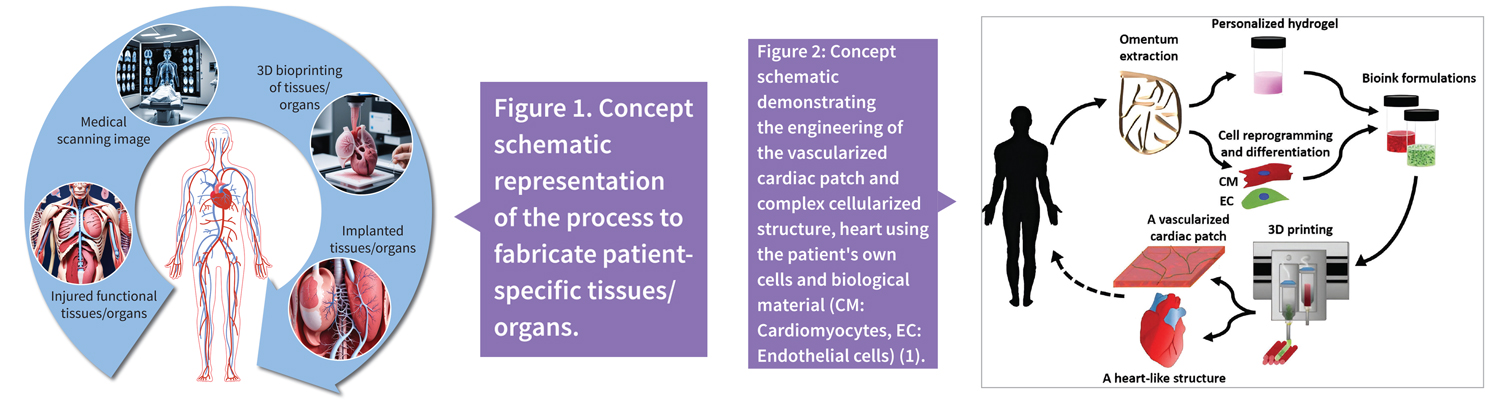
Nevertheless, a key challenge remains in the fabrication of a thick and three-dimensionally arranged vascularized implant. The human vascular system is a complex structure with a dense network of blood vessels ranging from the centimeter scale to the micrometer scale and is largely involved in the exchange of nutrients, oxygen, and cellular metabolic waste between the blood and the tissues. Another challenge is reducing the reaction of the foreign body (implants) with the patient. This can be done by modifying the surface properties of the implant and incorporating antiinflammatory drugs and bioactive molecules.
One consequence of engrafting 3D implants would also be visible signs of fever, pain, modulation in the patient’s vital test reports, inflammation at the surgical site, sometimes allergic reactions, etc. Hence, this is the main reason why medications are prescribed, the vitals of the patient are monitored, and the patient is kept under strict observation. Demonstrating a significant advancement, a research team led by Prof. Tal Dvir at Tel Aviv University successfully engineered a miniaturized and vascularized whole human heart out of a patient's own cells and biological material (Figure 2)!
Interestingly, the living cells in the bioprinted heart were contracting! In order to test the integrity of the different
compartments in the bioprinted heart, perfusion using colored dyes through the printed hollow chambers (right and left ventricles) and the septum in-between was demonstrated! This demonstrates the ability of the 3D bioprinting approach to engineer personalized tissues and organs, as an alternative to organ replacement in the future. Nevertheless, the cells in the bioprinted heart need to be trained to be able to work together to pump the entire heart. There are different ways to train heart tissue models or heart cells (called cardiomyocytes). The best possible ways are to electrically or mechanically stimulate and train them. For instance, with respect to electrical training, the tissues or cells are subjected to electrical stimulation at a range of frequencies and then the output is recorded. In addition, the various electrophysiological parameters are determined, analyzed, and compared to the native heart tissues.
Collectively, these strides in 3D printing/bioprinting emphasize its promising potential in cosmetics and pharmaceutical screening. It also provides an alternative platform for medical research in the fabrication and implantation of patient-specific complex tissue models/ organs, thereby saving thousands of lives.
The ultimate challenge lies in getting the organs to functionally work in a manner like how they usually do..
Thus, we can see that 3D printing/bioprinting, set towards clinical translation, is on the path to becoming a boon to medically challenged communities. Contributing to advancing scientific research in bioprinting, HiMedia Laboratories is the first Indian company to launch a Center of Excellence (CoE) for 3D Cell Culture Laboratory housing state-of-the-art facility for biomaterials and 3D bioprinting at Headquarters, Thane. Promoting such an academic-industry consortium would not only facilitate knowledge enhancement but expand a platform to motivate the young fresh minds to creative thinking generating innovative ideas leading to successful commercialization of biomaterials & bioinks, development of tissue models and its related biomedical research.
HiMedia Laboratories, already being one of the leaders in providing affordable and high-quality bioscience-based products has already started its journey through partnership with companies and eminent scientists in providing customizable 3D bioprinters as well biomaterials/bioinks, thereby, dedicatedly promoting the Make in India initiative. The state-of-the-art CoE facility provides a platform to students, researchers and professionals from different sectors to learn and gain hands-on-experience on different techniques and instrumentations involved in biomaterials/ bioinks development in a quicker and an affordable way.
References
- Noor, N., Shapira, A., Edri, R., et al. (2019). 3D printing of personalized thick and perfusable cardiac patches and hearts. Advance Science, 6(11), 1900344. doi: 10.1002/ advs.201900344. https://english.tau.ac.il/news/printed_ heart
- Organ Procurement & Transplantation Network, U.S. Department of Health & Human Services (United Network for Organ Sharing). https://optn.transplant.hrsa.gov/data/
- Hull CW, Apparatus for production of three-dimensional objects by stereolithography. https://patents.google.com/ patent/US4575330
- Aprecia Pharmaceuticals. https://www.aprecia.com/ news/first-fda-approved-medicine-manufactured-using- 3d-printing-technology-now-available
- https://www.nbcnews.com/mach/science/scientistsare- pushing-limits-3d-printing-these-shape-shiftingmaterials- ncna895301
- Steakholder Foods. https://www.steakholderfoods.com/ post/israel-s-steakholder-foods-unveils-industry-first-3dprinted- vegan-eel
- https://www.nbcnews.com/science/science-news/ surgically-implanted-3d-printed-ear-marks-medicaladvance- rcna31671